We recently had the opportunity to take a full tour of the ENVE Composites home base in Ogden, Utah. I attended along with our publisher, Dan Empfield, to see every step of how their products are conceived, engineered, produced, tested, and shipped.
We thought that the testing portion would be of particular interest to Slowtwitchers, and what follows is a photo essay of our afternoon spent at the ENVE in-house test lab. It’s an impressive place, with equipment for testing rim impact strength, fatigue, spoke pull-through, brake heat, and more. We were also surprised to find ENVE investing a lot of money into something they don’t even sell – tires. They have equipment for testing tire blow-off on rims, and even an innovative tool that measures tire bead diameter and stiffness. Even more interesting to Slowtwitchers, they recently constructed a massive rolling resistance test rig, and we got a front row seat to check it out.

The test lab is one large room on the second floor of ENVE’s HQ. They test many products beyond wheels, including forks, handlebars, and more.
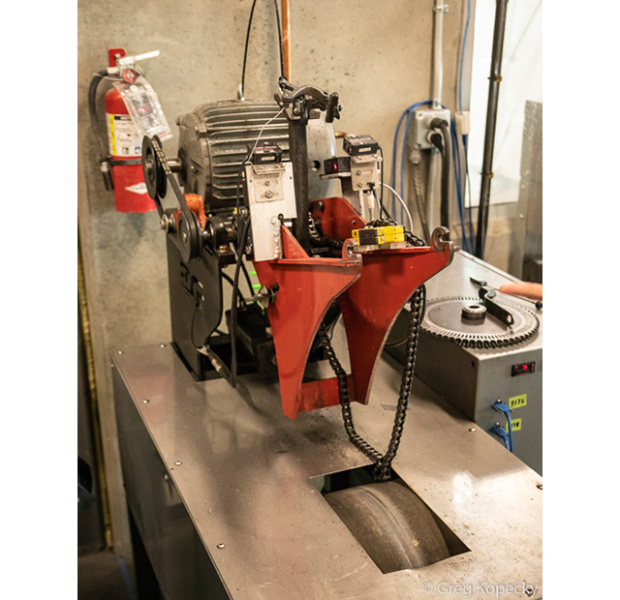
This is one test rig that doesn’t see a ton of action these days – the rim brake heat tester. While ENVE still produces a lot of rim brake wheels, much of the market has shifted to disc brakes. This device is chain-driven, and uses precise heat measurement tools. ENVE reports that their current rims have improved greatly over the originals from many years ago, with a new resin system resulting in no heat-related damage.
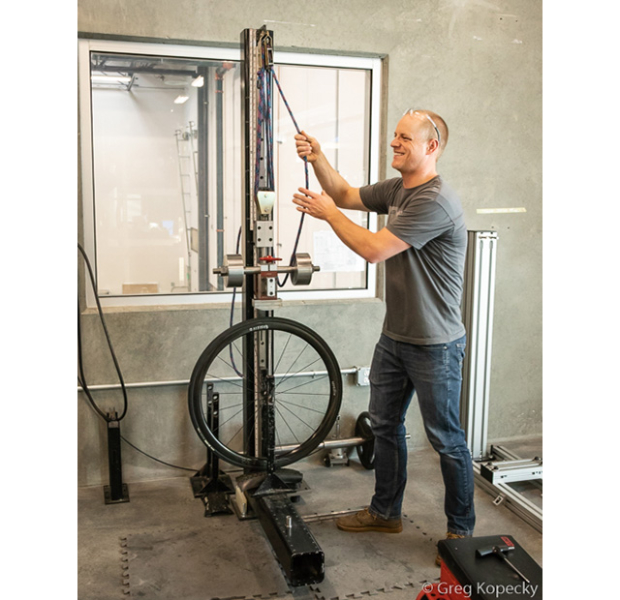
On to the fun stuff – breaking things. Here, Ike Pantone shows us their original impact test machine. It can be outfitted with different shaped impact surfaces, and loaded with different amounts of weight. We threw on a road wheel with a narrow tire, and slammed it repeatedly it until…

…a small crack finally appeared.
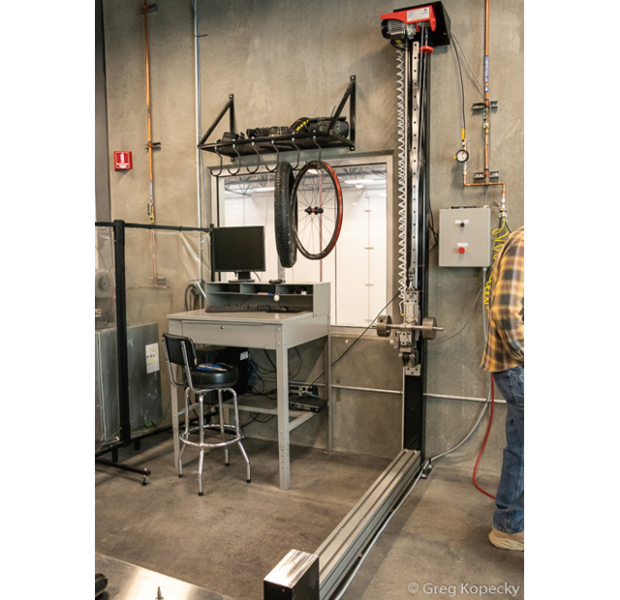
With further developments in their mountain bike wheels, that old impact tester simply was not tall enough to break the latest rims. A much larger and more automated impact tester was built, to up the impact ante (above).
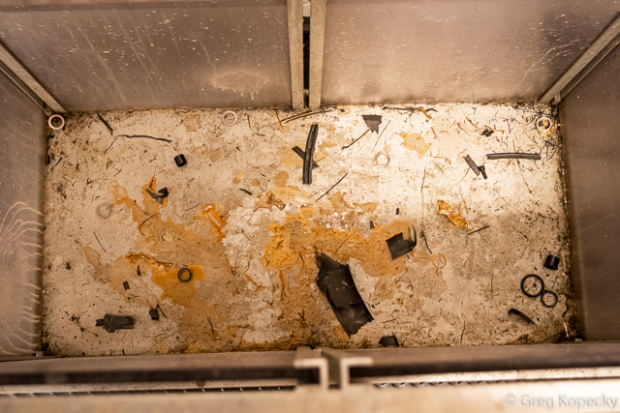
Next, it was time to talk tires – and break more stuff. This box was made to safely contain tire blowouts, and the debris you see above comes from tire sealant and blown-out hub parts (the impacts are so dramatic that hub end caps and pieces come flying out, since they’re not constrained in the dropouts of a bicycle).
The short video above shows our test of a road wheel with a big 32mm tire. It got all the way up to 140psi before the tire bead failed – way beyond the maximum pressure of the system.
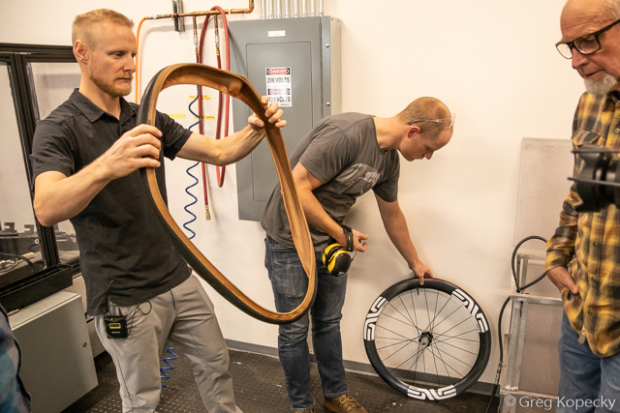
ENVE’s Jake Pantone inspects the tire bead, which is now completely useless. The blowout was incredibly loud (we wore ear plugs), and they report that fat bike tires shake the entire building upon failure.
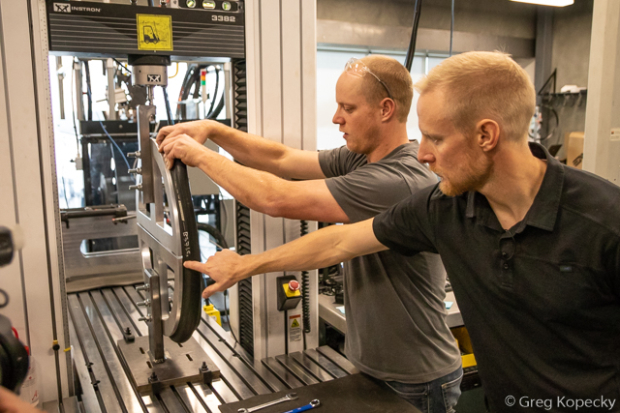
Next up, ENVE created a really innovative tool that tests tire bead diameter and stiffness. We’ll get in to more detail on this topic in a later article, but the short explanation is this: ETRTO specifies a huge number of constraints for rim manufacturers, but not tire manufacturers. In the interest of consumer safety (and, of course, limiting liability), ENVE tests as many tires as they can get their hands on, to ensure that they’ll stay safely mounted to their rims. They shared the results with us, and we were shocked to see a huge variability in both tire bead diameter and stiffness. We’ll share data as we get it, but take our word for now that tires are far from created equal.

The tester splits in the middle, forcing the tire bead to stretch. Their protocol is based on the original Mavic tubeless tire testing protocol, which they say is the best-established standard. Our hope at Slowtwitch is that this can eventually become an actual ISO test for tire manufacturers, since no such test is currently required.
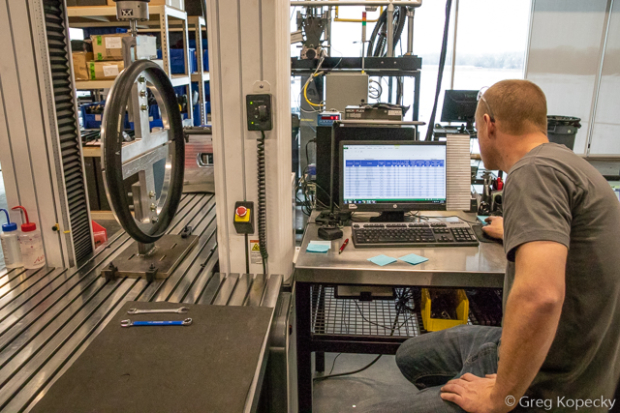
Data is recorded on this computer, which ENVE compiled into an X and Y grid of bead diameter and stiffness. This is all important because tubeless bicycle wheels are moving towards hookless rims, which is the tubeless interface used by all other industries (i.e. automobile, motorcycle, etc). This design relies on an interference fit between the bead seat portion of the rim and the tire bead – which requires precise manufacturing of wheels and tires. We witnessed the production of ENVE’s rims and the different tooling for their hookless rims, giving a much more consistent bead seat diameter than hooked rims. If, however, the tires are not made consistently to a certain diameter and stiffness, they can still blow off the rim – and rim bead hooks add an additional failsafe. ENVE’s position is that if all tires were made to sufficient manufacturing standards, we could all benefit from the other positives of hookless rim construction, such as lighter weight and improved impact strength.
If a tire is too big, stretches too much, or has too much variability from tire-to-tire, ENVE does not recommend it for their hookless AR rims – and they have a list of approved tires on their website. Note that their standard SES road wheels are tubeless compatible, have bead hooks, and can be used with any road tire.

We saved the best for last, and that’s ENVE’s brand-spanking-new rolling resistance test rig. This behemoth is still being finished and calibrated, so we do not have any shocking data-bombs to drop on you just yet.
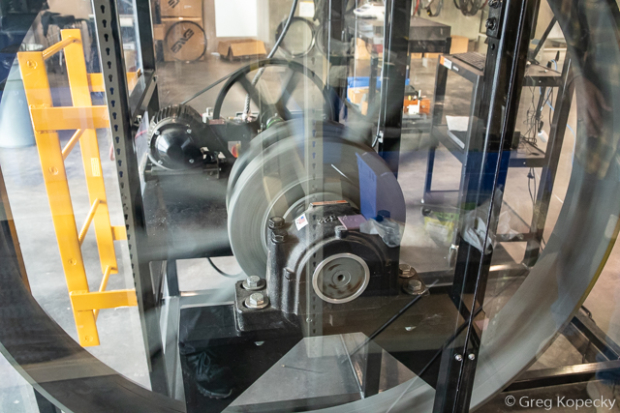
What we can tell you is that this is a serious piece of equipment, driven by a giant-size wheel. ENVE wanted to create something that would be as close to a flat road as possible, because much of the current data is from small-diameter roller testing.
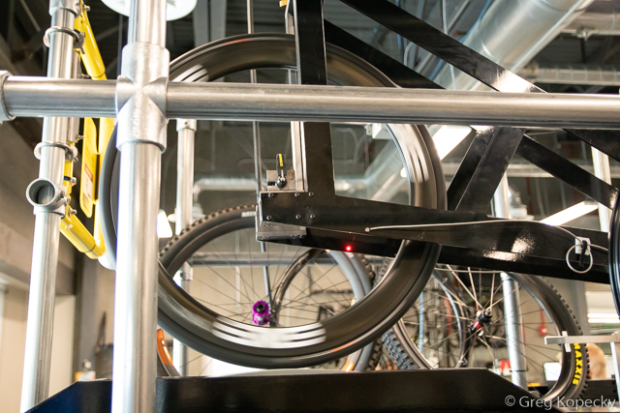
The giant drive wheel turns a bicycle wheel on the top of the machine, which can be easily swapped out.

Worried that a smooth drum isn’t real-world? ENVE showed us several sample ‘treads’ for the drum, which can be installed to simulate different road surfaces. We know that Slowtwitchers get more excited about rolling resistance data than Christmas morning, so we look forward to what this machine will provide.
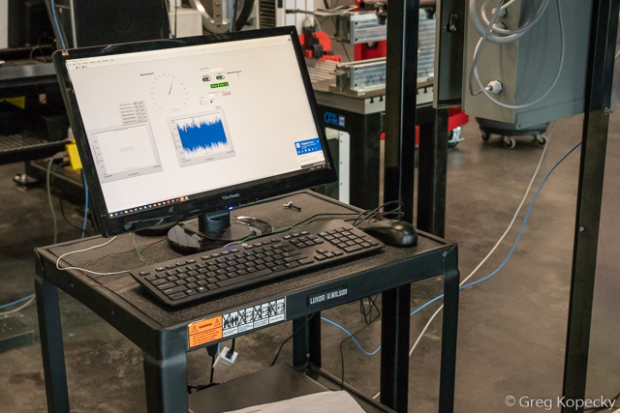
Everything will be compiled and stored on this computer, and we hope to have many detailed Crr charts to share with you.
In the coming days, we’ll have a second gallery for our tour of their massive factory, which is responsible for making their own tooling, countless small parts, injection-molded plastic pieces, painted parts, and of course – wheels, carbon hubs, frame tubes, and more.